New printing technologies offer innovative solutions for personalised medicine and tailored dosage forms to meet the needs of individual patients.
With an increasing awareness that different patient populations (newborns, children, adolescents, adults, elderly) require different dose regimens, and that individualised drug therapies increase the compliance of patients, healthcare professionals also face challenges regarding the efficacy and success of a therapy.1,2
By creating a platform technology to design individual dosage forms for particular needs (low or high drug loads, systems for immediate or sustained drug release), which enables flexible dosing opportunities, new concepts can be provided to deliver active pharmaceutical ingredients (APIs) to the patient. Thus, new and intelligent drug delivery systems are needed to overcome the hurdle of poor compliance and to provide flexible dosing opportunities for a broad population of patients. In this context different printing technologies can play a role.
Printing technologies and challenges
Printing technologies have emerged as potential techniques to solve several issues with regard to the dose delivered, and the size and the shape of a dosage form.3 In recent years, solutions for tailoring the delivered dose for specific patients and patient groups by means of, for example, inkjet and flexographic printing have been shown.4–7 These printing technologies were modified to produce solid dosage forms by printing inks with APIs on solid substrates. These approaches were ground-breaking with regard to flexible and individual dosing.8 The application of three-dimensional (3D) printing offers the opportunity to print the entire dosage form based on digital design. After the first commercialisation of a 3D printing technique in the 1990s,9 a number of techniques exist to date and are suited for varying purposes (Table 1).
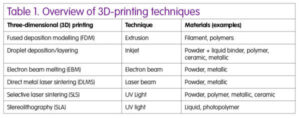
The challenge from a pharmaceutical point of view and the objective in the latest research in drug delivery is the choice of appropriate pharmaceutical excipients in these printing processes to provide suitable drug carriers and matrices. Recent news of the United States Food and Drug Administration (FDA) approval of a 3D printed drug (Spritam) shows that a printing technology can be a viable choice of manufacture and construction of drug delivery systems of the future. The advantage of this specific product is the creation of a highly porous matrix and the optimised design of the tablet enables a faster onset of disintegration and drug release than the conventional tablet derived by compression. This shows that printing technologies are viable options for changing manufacturing.
Inkjet and flexographic printing has already been successfully used to print APIs on edible and orodispersible polymer films.5,6 Accurate deposition of the material in the printing process is desired to be precise to create tailored drug delivery systems. The amount of released drug and the drug release properties can be modified by creating systems with variable sizes, density and surface area by means of the computer-aided design of the dosage form.
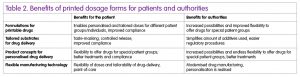
Hot-melt-extrusion-based 3D printing therefore has its origin in a well-known process combining the challenges of engineering and process technology with the high standards for accurate dosing of pharmaceutical actives to achieve promising new options in dosage form design and drug delivery. If printing as manufacturing technology is used to produce products of variable sizes and shapes, multifunctional structures can be created to enable further complexity and a high level of sophistication, for example with regard to drug release properties. The latest described concepts include advanced multi-layer coatings, stacked systems, and integrated bioactive multi-compartments, which comprise of integrated combinations of diverse materials to form sophisticated biofunctional constructs.10
Perspective for tailored drug therapies
Printed dosage forms will be created to exhibit tailored local and systemic therapeutic effects through the oral route of administration with viable extension potential. The concept of fabricating prototype drug delivery systems through the combined utilisation of printing technologies will solve existing manufacturing challenges around low dose, flexible dose and also potentially for multi-drug products in a totally new manner. The approach will also be more environmentally safe, for example through less waste generation, energy and solvent savings, and efficient containment. The fact that individualised dosing will be made possible will create entirely new opportunities for dispensing medicines from pharmacies and dosing of substances at hospital pharmacies or wards opening up totally new concepts for point-of-care medications.12,13
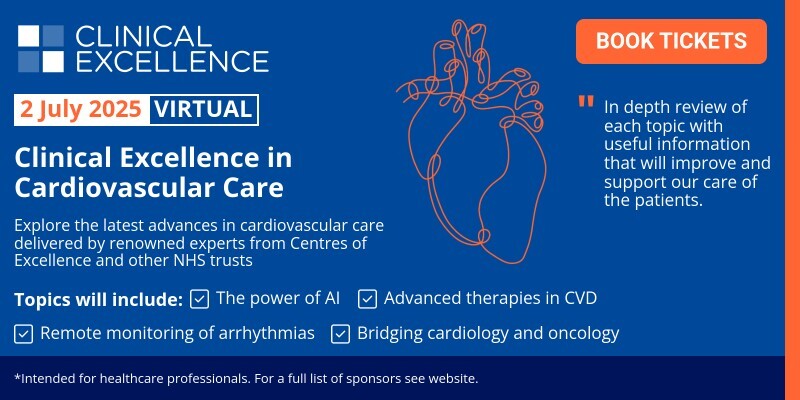
Pharmacies could dispense individual multiple-drug doses directly to patients using printing technology. In particular, paediatrics could profit from this innovative approach bridging the existing gaps in licensed paediatric medicines, extemporaneous preparations, and off-label use. Hospital pharmacies would have the ability for efficient computerised and contained tailored dosing for treatments with different dosing regimens and varying levels of therapeutic complexity.
Fig. 1: Personalising dosage forms by means of printing technologies in hospital pharmacies
When hospital pharmacies were equipped with printing units, dosage forms for an individual patient can be produced on demand (Figure 1). By using drug-loaded polymer filaments, which could be obtained from pharmaceutical manufacturers, for example, with different release properties and drug loads, 3D-printed dosage forms could be produced with the size and dosage required for a certain patient. Furthermore, surface printers such as inkjet printers, which are equipped with a container of drug-loaded ink, enable the deposition, in particular, of low-dose drugs and even combinations of those by printing pre-defined pattern and layers.
Edible substrates such as sugar paper sheets or orodispersible films (usually thin sheets made of hydrophilic polymers) not only offer a suitable printing surface, the natural sweet taste of sugar-based materials or the incorporation of taste improving agents (for example: sweeteners, flavours, masking agents) but may also improve the compliance of the patient.14 Fast oral disintegration of the substrate material can be advantageous for patients who face swallowing issues. Nevertheless it is also possible to place the printed doses in a capsule that can be administered to the patient.8
It becomes obvious that printing technologies offer multiple options to make drug therapy more efficient and less cost-intensive. In particular, for hospitals, this emerging technology will enable the provision of tailor-made and personalised dosage forms for individual patient needs on demand. Pharmacists in the hospital pharmacy can decide together with the physician in charge the most suitable dosage form for a patient. The pharmacist and physician can consider the drug or drug combinations that are required for a successful treatment. Furthermore, measures can be taken to adjust the amount of the required single doses, which fits the individual patient’s needs to design and produce the individual dosage forms by means of printing.
Conclusions
By creating a platform technology to design individual dosage forms for particular needs, which enables flexible dosing opportunities, new concepts can be provided to improve drug therapies. Printing technologies will enhance drug therapy by enabling the provision of personalised designs (for example, size of dosage form) and doses for patients who require an individual dose regimen. They will be created to exhibit tailored local and systemic therapeutic effects through the oral route of administration with viable extension potential.
Individualised dosing enabled by printing will create entirely new opportunities for dispensing medicines from pharmacies and dosing of substances at hospital pharmacies or wards opening up totally new concepts for point-of-care medications. Hospital pharmacies would have the ability for efficient computerised and contained tailored dosing for treatments with different dosing regimens and varying levels of therapeutic complexity.
Key points
- Individualised dosing of drugs enabled by printing will create new opportunities for dispensing medicines in hospital pharmacies or wards.
- The use of printing technologies opens up totally new concepts for point-of-care medications in the hospital setting.
- Hospital pharmacies could have the ability for efficient computerised and contained manufacture for specific patient groups by printing technologies.
- Printing technologies can solve existing manufacturing challenges around low dose, flexible dosing and provide solutions for multi-drug products.
- Different printing technologies will enable the provision of tailor-made and personalised dosage forms in the future.
Authors
Maren Preis PhD
Niklas Sandler PhD
Pharmaceutical Sciences Laboratory, Åbo Akademi University, Turku, Finland
Email: [email protected]
References
- Preis M. Orally disintegrating films and mini-tablets – Innovative dosage forms of choice for pediatric use. AAPS PharmSciTech 2015;16(2):234–41.
- Breitkreutz J, Boos J. Paediatric and geriatric drug delivery. Expert Opin Drug Deliv 2007;4(1):37–45.
- Kolakovic R et al. Printing technologies in fabrication of drug delivery systems. Expert Opin Drug Deliv 2013;10(12):1711–23.
- Buanz ABM et al. Preparation of personalized-dose salbutamol sulphate oral films with thermal ink-jet printing. Pharm Res 2011;28(10):2386–92.
- Genina N et al. Tailoring controlled-release oral dosage forms by combining inkjet and flexographic printing techniques. Eur J Pharm Sci 2012;47(3):615–23.
- Janßen EM et al. Drug-printing by flexographic printing technology – A new manufacturing process for orodispersible films. Int J Pharm 2013;441(1-2):818–25.
- Meléndez PA et al. Thermal inkjet application in the preparation of oral dosage forms: Dispensing of prednisolone solutions and polymorphic characterization by solid-state spectroscopic techniques. J Pharm Sci 2008;97(7):2619–36.
- Sandler N et al. Inkjet printing of drug substances and use of porous substrates-towards individualized dosing. J Pharm Sci 2011;100(8):3386–95.
- Rowe CW et al. Multimechanism oral dosage forms fabricated by three dimensional printing. J Control Release 2000;66(1):11–7.
- Preis M, Breitkreutz J, Sandler N. Perspective: Concepts of printing technologies for oral film formulations. Int J Pharm 2015;494(2):578–84.
- Repka MA et al. Applications of hot-melt extrusion for drug delivery. Expert Opin Drug Deliv 2008;5(12):1357–76.
- Visser JC et al. Orodispersible films in individualized pharmacotherapy: The development of a formulation for pharmacy preparations. Int J Pharm 2015;478(1):155–63.
- Pardeike J et al. Nanosuspensions as advanced printing ink for accurate dosing of poorly soluble drugs in personalized medicines. Int J Pharm 2011;420(1):93–100.
- Krampe R et al. Oromucosal film preparations: points to consider for patient centricity and manufacturing processes. Expert Opin Drug Deliv 2015:1–14.