teaser
Stephen Cook
Director of Pharmacy
East Kent Hospitals
NHS Trust
E:[email protected]
E:[email protected]
The pressure is on. A modern hospital pharmacy has to meet medical and financial demands in a competitive market. In order to do this, repetitive tasks are scrutinised. The delivery of medications to the hospital ward is one such repetitive task, and one that is carried out several times a week.
By automating order picking, highly trained pharmacy staff are relieved from these tasks and can perform other valuable pharmacy duties. With the service level having been increased and being more efficient, delivery frequency can be raised. At the same time, these services can be made available outside of the hospital. Reducing costs while increasing productivity is possible. In Germany, over 15 MDS (Medium Dispensing System, P@P Picking Systems GmbH; see Boxes 1 and 2 and Figures 1 and 2) demonstrate that it is possible to achieve this.
[[HPE22_box1_63]]
[[HPE22_box2_64]]
[[HPE22_fig1_63]]
[[HPE22_fig2_64]]
The East Kent Hospitals NHS Trust experience
The East Kent Hospitals NHS Trust has also made this possible in the UK.
In this pharmacy department, order picking is now close to being fully automated, and the systems are being integrated into the daily pharmacy business. Systems of this type raise the overall quality of patient care. Centralised distribution allows for the supply of the three major acute hospitals of the trust. Overall stockholding costs are thus reduced across the trust.
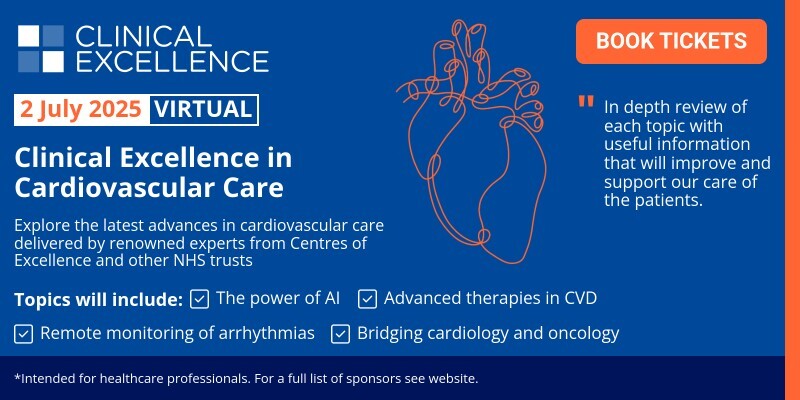
In Europe, there is currently a trend towards centralisation. Cost cuts make the work of the pharmacy departments even more valuable. Automation and streamlined logistic process help to optimise the hospital performance as a whole.
Improved staff utilisation and centralised distribution were key factors when deciding to automate at the East Kent Hospitals NHS Trust. Inhouse logistics have been adapted to meet the new requirements. Wards now receive required medication and other items in ward boxes that have been automatically filled by the MDS. Any product that cannot be handled automatically, such as bags, is added to the shipment manually after the robot has completed the picking run.
Stock levels in the MDS are set to meet the needs of two weeks. This gives one member of staff the chance to replenish at times that suit the daily routine.
Replenishment
Experience shows that large systems require a fast and efficient replenishment process. A piece-by-piece solution cannot provide this.
With the MDS, replenishment is possible at any time and does not reduce the output of the system. Handheld terminals support the replenishment process and ensure high handling accuracy. As product channels are filled from the back of the system, the first-in/first-out principle applies. Stock levels are constantly monitored by the system and, if an empty channel or a low stock level are detected inside a channel, they are immediately reported. A feature will soon be added to the system whereby a light will show empty locations in each channel. This will lead to a faster and even more efficient replenishment process.
Average time for automated replenishment is currently 10 seconds (to final location). Thus, 2,500 pieces require about seven hours to replenish. Depending on the configuration, picking can take as much time, which means that a system could operate for up to 14 hours a day. The MDS needs about three hours to pick the same quantity, and manual replenishment is carried out in two hours at any time.
Changes for staff
Implementing automation in a hospital pharmacy is a process that requires efforts from all staff involved.
Senior pharmacy staff and specialists from the companies providing the systems have to work out an ideal solution combining the know-how from both parties.
Pharmacy and technical staff are being kept up to date with the different developments. Automation should be seen not as a threat but as a valuable tool to support daily business. Once the automated system is up and running, pharmacy staff should be able to spend more time on consulting and pharmacy work, rather than on picking and packing.
Conclusion
Automation will allow pharmacy departments to be one step ahead. Cost reductions and better patient care are the major benefits.