teaser
Stefan Harms
MSc
Doctoral Candidate
Department of Logistics
University of Dortmund
Dortmund
Germany
E:[email protected]
These days, it is nearly impossible to open a professional journal from the fields of logistics, economics or production technology and not come across the topic of radiofrequency identification (RFID) technology. These articles invariably invoke the allegedly enormous advantages of RFID, and one is often under the impression of standing on the brink of a revolution in information technology. However, when the critical observer takes the time to look behind the façade of euphoric media coverage, major marketing campaigns and convincing promises of system performance, a different, more sober picture emerges. This article evaluates RFID technology from the critical perspective of a logistician in the pharmaceutical industry.
Technology
RFID describes a technology that allows for communication between a transponder (tag) and a read/write unit (RW unit) with magnetic or electromagnetic waves. The basic intention of RFID is to attach a transponder to movable goods and read and modify data at any point in the supply chain. There are two types of RFID technology, with the following distinguishing characteristics.
For systems in the low-frequency (LF; 125kHz) and high-frequency (HF; 13.56MHz) ranges, a magnetic field is created by an antenna attached to the RW unit. As soon as a transponder reaches the magnetic field, electricity is introduced into its antenna, thus allowing the transponder chip to communicate with the RW unit. Although in this case there is technically no transmission of radiofrequency (but rather transmission via magnetic fields), the term RFID has nonetheless been adopted for such systems. Systems operating in the LF and HF ranges tend to operate passively – that is, the energy needed to operate the transponder chip is taken from the antenna of the RW unit. The maximum effective RW distance is therefore limited to 1.5m, depending on the size of the antenna of the RW unit and the transponder. Such systems rely on the principle referred to as “inductive coupling”.
For systems in the ultrahigh frequency (UHF; 868MHz) and short high-frequency (SHF; 2.45GHz) ranges, the antenna of the RW unit emits radio waves, which are received and modulated by the transponder. RFID technology in the UHF and SHF ranges is available as an active or passive system. In passive systems, the transponder receives the energy for operation from the antenna of the RW unit and can achieve a transmission range of up to 6m (with 4W in the USA). Active transponders contain a battery used for the operation of the transponder, including, with some systems, the sending of the response signal. The read distance on active systems can reach up to 100m; additionally, a much higher volume of data can be stored on the transponder chips compared with passive systems. The functional principle of such active systems is also referred to as “backscatter coupling”.
In addition to the different functional principles, varied methods of energy supply and multiple RW distances, there are further distinguishing characteristics of the passive and active systems. For example, the higher the frequency, the higher the speed of transmission between the RW unit and the transponder. However, with higher frequency comes greater systematic sensitivity to metal and water.
Advantages and disadvantages
Compared with other identification systems, RFID systems have the following advantages:
- They can deal with very high volume – depending on the RFID system in use, up to 100 transponders can be read simultaneously.
- Each transponder chip is marked with a unique identification (UID) number, allowing for clear, unambiguous product identification.
- Via radio interface, transponders can be read through most – but not all (see disadvantages) – materials (cardboard, plastic, wood, dirt, etc).
- Information placed on RFID transponders may be altered as often as required.
- Compared with barcode labels, RFID transponders are more durable and have a longer lifespan. Passive systems allow for up to 100,000 RW cycles. The battery life of active systems, while strongly dependent on the frequency of RW processing, can be as high as seven years.
However, this technology involves several systematically inherent and fundamental disadvantages:
- The many different transponder technologies and transmission processes and a rather slow move towards standardisation impede a fast and comprehensive distribution of RFID technology.
- No RFID system is capable of transmitting through metal; liquids, on the other hand, interfere with the transmission of UHF and SHF waves. A direct application of passive UHF and SHF transponders on metal and liquids still does not allow for these products to be recorded. The effect of liquids on LF and HF systems is minimal, yet direct application on metal reduces the recording range significantly (with LF systems) or makes registration impossible (with HF systems).
- The parallel alignment to the antenna can have a marked effect on recording distance, especially in the HF range. Without costly special antenna configurations (which are still somewhat unreliable), HF transponders cannot transmit or be read, even when at the right angle to the antenna.
- At €0.40 each per passive system and €0.50 each per transponder, RFID technology is generally much more expensive than barcode systems, especially for linear logistics and production applications. The higher fixed costs for RW units, antennas and interface software also prove to be a significant disadvantage.
- A location, in the strict sense of determining the exact X–Y coordinates of a transponder using direction finding, is not possible with passive systems. Only some special, active systems can determine location (with an accuracy of within 3m).
In recent years, various RFID systems have come on the market with functions above and beyond the typical data transmission abilities:
- Transponders equipped with pressure sensors are able to measure the tyre pressure on cars and transmit this information to a receiver in the chassis.
- Transponders with integrated temperature sensors have been introduced to the grocery industry as a way to monitor the “cold chain” for perishables.
- Certain active systems, which allow for location within 3m, are used by car makers to track the location of new vehicles.
The legend of RFID
RFID technology is far from brand new. Active transponder systems were used as early as the Second World War for airplane identification. RFID technology has been used regularly since the 1970s and 1980s, particularly in the areas of animal identification, production control and inventory management.
There are several different reasons for the substantial current interest in RFID technology by nearly all branches of industry:
- Increased competition and growing globalisation have led to more complex logistics and information networks. With the help of RFID, businesses hope to automate the logistics process and meet the growing demand for accessible, up-to-date information.
- Within the framework of the EU law for food safety (EU directive 178/2002), RFID technology was seen as a possible way to automate the product tracing process.
- With the development of reasonably priced passive HF transponders and very efficient passive UHF transponders over the last several decades, many hoped to access further areas of application with RFID technology.
Nonetheless, sales of RFID products remain quite sluggish because:
- There is still no universally applicable RFID technology available.
- Specialised knowledge is still required to determine the best-suited RFID technology for any given application.
- Achieving a return on investment (ROI) remains challenging, particularly for businesses with linear logistics processes.
- RFID suppliers take no responsibility for production interruption and losses caused by RFID technology.
- No sound concept has been created for the management of the enormous amount of data created.
- Significant uncertainties remain with regard to the acceptance of new standards and technology.
For these reasons, various major producers, suppliers and potential users of RFID technology have attempted to stimulate the demand for RFID products and escape the “chicken–egg problem” (potential RFID technology users seek lower system costs, particularly for transponders, in order to implement on a large scale; producers, on the other hand, argue that only higher demand can reduce costs). They have used the following strategies:
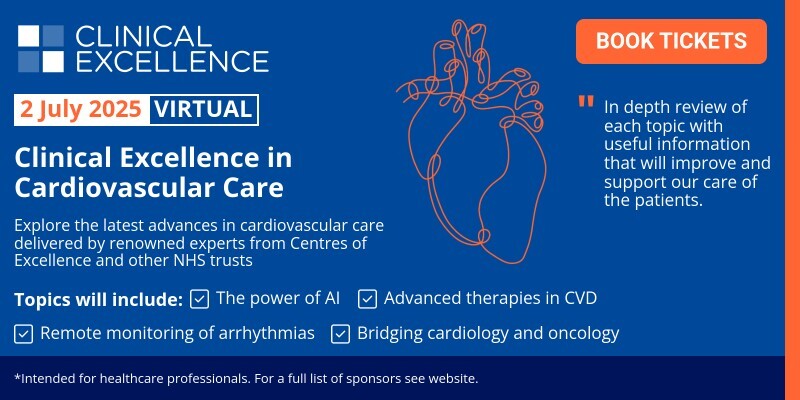
- Major marketing campaigns.
- Exaggerated portrayal of the efficiency of RFID systems.
- Launching of overly optimistic press releases.
- Concealment of technical problems with the system.
- Publishing of new studies underestimating transponder pricing (for example, in 2002, a study predicted that transponders would cost €0.05 by 2005).
- The constant announcement of new pilot projects.
This led to:
- Significant expectations, which RFID technology often cannot meet.
- Growing uncertainty among potential RFID technology users.
- Increased public concern with regard to privacy and security of private data.
RFID in the pharmaceutical industry
Nonetheless, more and more pharmaceutical companies are showing a guarded interest in the application of RFID technology.
Improving the supply chain
By equipping products, pallets or loading units with transponders, businesses can speed up the processes of product identification and confirming that shipment has been completed, at the same time eliminating the need for opening the packaging for visual confirmation.
Efficient control of the fulfilment process
Errors in the fulfilment process in wholesale, hospitals or pharmacies often have serious consequences for patients. Products equipped with a transponder could be automatically tracked during the distribution and fulfillment process, leading to easy and quick inventory control and ensuring that pharmaceutical prescriptions are dispensed correctly.
Detecting and combating counterfeit pharmaceutical products
In its report Combating Counterfeit Drugs in February 2004, the FDA determined that a growing number of counterfeit pharmaceutical products were appearing on international markets. A primary reason for this is the often fragmented and multilayered logistics process.
The FDA views RFID technology as one of several possibilities – with the use of the unique and counterfeit-safe transponder number – with strong potential for securing the supply chain. However, the FDA does not currently view RFID as ready for widespread commercial use.
Tracking producers and batch numbers
With the help of the unique transponder number and an international database, date and location of production could easily be traced with RFID technology.
Additionally, one could determine where other products from the same batch were shipped, making targeted recalls more efficient. The production data could also be stored on the chip in such a way as to be easily read by recipients via their RW unit.
Theft controls
Using RFID technology, each step of the distribution process of pharmaceutical products could be recorded and monitored, thus making product theft easy to trace. If all outgoing shipments from a warehouse were equipped with RFID antennas, any diversion of product would be recorded and reported.
Cold chain monitoring
Transponders equipped with temperature sensors and batteries to allow for continual temperature measurement could be employed to monitor the cold chain during shipment. Compared with traditional data loggers, RFID transponders have several advantages. First, with a relatively low price of €8 each, they are cheaper. Additionally, one can read several transponders simultaneously, and through many materials (no loss of cold due to opening of containers). Reading the temperature of the transponder via radiotransmission allows for close temperature monitoring throughout the shipping process, rather than only at its final destination. For example, if a shipment exceeds the mandated shipping temperature during transit to the airport, this can be noted before loading the shipment into the airplane. Transport can be stopped and, this way, time and money related to further transportation and return transport can be saved.
Despite this promising potential, there are many obstacles to comprehensive use of RFID technology, particularly as an “across the board” solution:
- Aluminium foil in packaging and liquid pharmaceutical products may disrupt or even completely prevent communication between the transponder and the RW unit.
- The effects of radiofrequency waves on “live” pharmaceutical products have yet to be determined.
- The added value derived from transponder use as compared with barcode labelling does not justify the much higher cost of transponders (smart label: €0.40; barcode label: €0.03).
- The creation of a comprehensive RFID logistics system would require RFID infrastructure at all points along the supply chain, which would be cost-prohibitive. One possible alternative is the development of active transponders that are Bluetooth (BT)-compatible, since nearly every modern computer has access to a BT-RW unit.
- The construction of a comprehensive RFID infrastructure is also made more difficult by the fact that efforts towards standardisation have only slowly borne fruit, and no one knows which RFID technology will be used in which branch of industry, and with what applications.
Yet many experts still believe that the pharmaceutical industry will be a trailblazer with regards to the introduction of RFID technology to transport and logistics. They cite the following reasons:
- Logistics processes are becoming increasingly complex, particularly in the pharmaceutical industry. The need for an active information control system such as RFID is greater than ever before.
- Compared with other branches, the use of RFID technology brings more added value to the pharmaceutical industry. In addition to the basic tracking of products and collection of data, the RFID technology allows the pharmaceutical industry to identify counterfeit products, avoid errors in fulfilment of prescriptions, simplify recalls and monitor the cold chain during shipment.
- Due to high product values and the potential costs and liability associated with shipping errors, the pharmaceutical industry has higher margins and is less price-sensitive (for example, in the case of transponder costs) than other industries.
Conclusion
Many pharmaceutical firms have recognised the potential of RFID technology and have begun to explore its use. This interest is reflected by the many pilot projects being conducted by firms in cooperation with third-party system integration companies and universities.
As technological advances are made, it is likely that state regulation agencies will turn to RFID technology as a medium for the implementation of new regulations and standards. One needs only look to the many state-funded research projects focused on cold chain monitoring via RFID. However, anyone interested in RFID implementation must be aware of the potential risks and difficulties contained in such a project. In any case, one must consult with a neutral expert on the subject and maintain the necessary critical distance throughout every phase of the project.